SPS is the leading trade fair for smart and digital automation. More information on the trade fair website.
Research to develop the battery fuses of the future
Battery systems and DC power supplies are becoming increasingly important and a new standard for matching fuse links is due for publication soon. However, SIBA has already teamed up with TU Dresden to develop fuses for these applications that can perform better than the standard requires.
The research teams from SIBA and the TU Dresden University Department for High Voltage and High Current Technology are still in the mid-point of their joint research project 'Development of a full-range fuse link with enhanced reliability for use in the energy supply network of the future'. Nevertheless, they have already gained valuable information, according to qualified engineer Lukas Büttner, who is content head of the project at the TU and whose team has already been assessing the first sample fuse elements. Here the focus has been on the soldering point, which in the case of NH fusible elements for battery fuses is responsible for the cut-off at overload. 'It was found that the breaking behaviour is influenced by more factors than just by the temperature of the solder. In contrast to previous assumptions the geometry of the fusible element, for example, plays a crucial role on reliability in this area.'
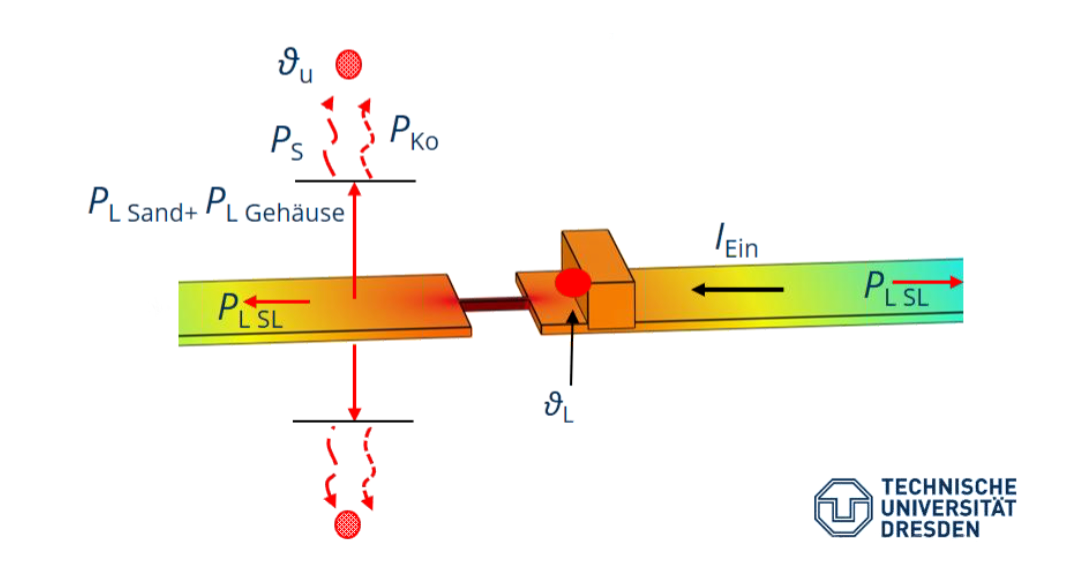
by the temperature of the solder
So if you want to make fuses like SIBA's, which when fitted to energy storage systems do not cut out prematurely after five years because the high loads present have caused them to age too rapidly, you now have another interesting design reference point to work from. And practice-oriented research of this kind is precisely what this collaborative project is all about, with SIBA and TU Dresden having already secured the necessary funding from the BWM (Federal Ministry of Economics) Central Innovation Programme for SMEs (ZIM). The state has been providing support for the ZIM in order to ensure that German SMEs stay ahead of the international competition.'The funding decision came through in June 2020 and we started our project soon afterwards', explains Dr Jens Weber, SIBA's Head of Development, as he goes through the sequence of events. Of course the two teams could only actually meet up once last summer, but since then they have been holding video-calls every one to three weeks. 'We have lively exchanges', says Weber, 'and so we are very much on schedule'. The programme was set to run for 20 months and by early April had nearly reached the half-way mark. Both partners are certain that the knowledge gained to date will lead on to promising long-term tests. With this in mind SIBA has recently provided the TU research team with new sample fuse elements. 'We are now looking at how the soldering point behaves under high and persistent loading', says Büttner. At the same time the researchers are making the most of the university department's existing expertise. In the words of group leader Dr.-Ing. Christian Hildmann: 'In addition to the know-how that our 'electrical contacts and connections' group has developed, the department also has a great deal of research experience with heat flow in electrical components.' In the second half of the project the research team will use thermal network methods and metallurgical investigations to examine how the solder material and the fuse element interact with each other over a long period of loading. SIBA will then be able to use its expertise to optimise production of the overload restriction point.
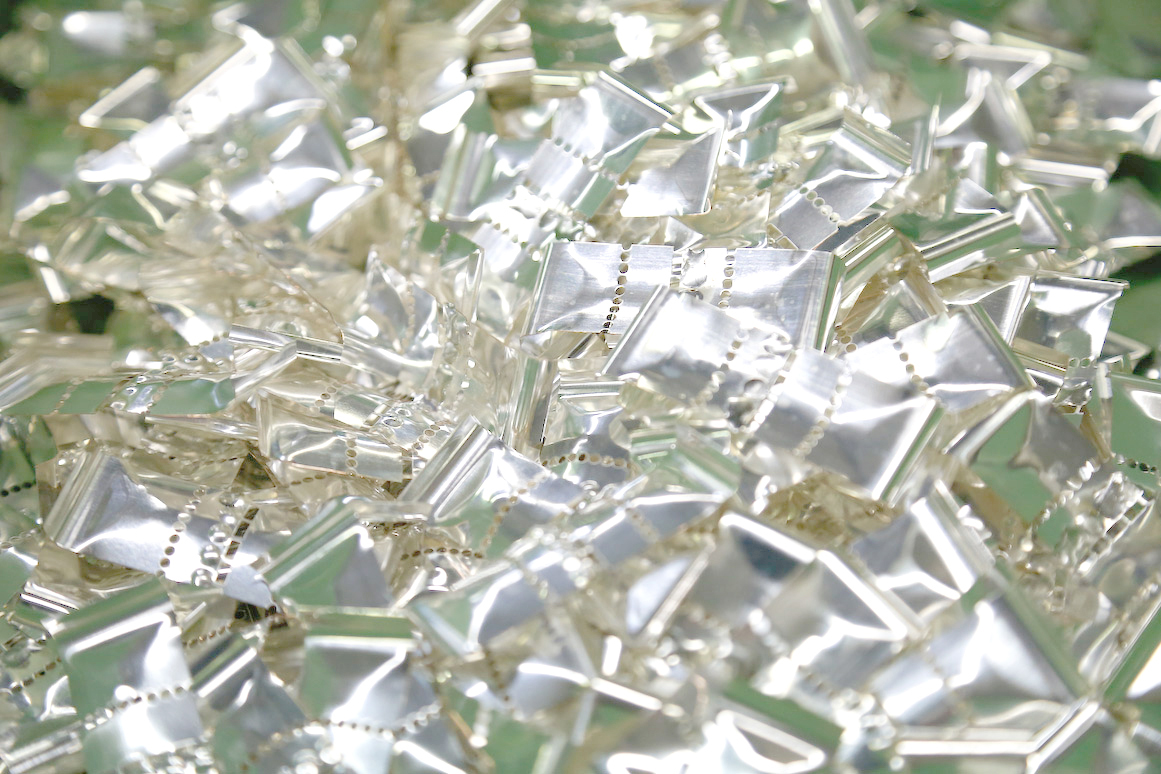
material and the fuse element interact with each other over a long period
In theory such projects can even result in patents being taken out, but according to Hildmann this is unlikely in this case. Even though new correlations have indeed been discovered 'we also anticipate that the parameters will vary enormously in practically each individual case', says Hildmann. Nevertheless, what is emerging is a methodology of real practical applicability whereby fuses for energy installations and similar operational purposes can be produced more quickly and more efficiently in line with their specific performance characteristics. 'That is what we need and that is what can give us a competitive edge', says SIBA development manager Weber. For in order to meet the ever-increasing demands associated with energy storage systems and with the coming DC power supply in factories, end-users need fuses that are long-lasting and yet will cut out exactly when required. The new standard for battery fuses (DIN EN 60269-7 VDE 0636-7), whose final version is soon to be published, will among other things introduce a separate utilisation category – known as gBat. Thanks to its collaboration with the scientific community SIBA will now be in a position to produce new gBat fuses that perform better than the standard requires.